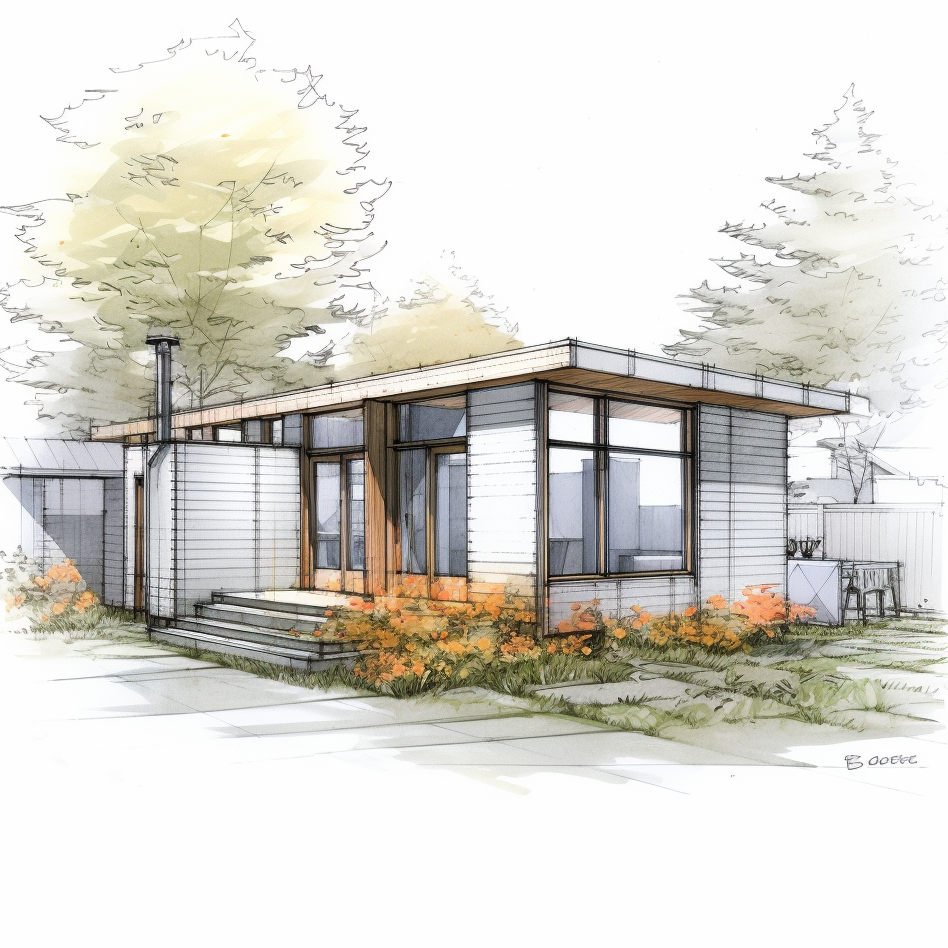
At LOGIC Building Systems, we were excited to see the recent NY Times Op-Ed piece, “Why Do We Build Houses in the Same Way That We Did 125 Years Ago?” After studying the modular building space for almost a decade, it was encouraging to see a major news outlet tackle one of our favorite topics. Consequently, we had a pretty good idea of what author Binyamin Appelbaum got right. Equally important, we observed some critical misses, which could impact billions of dollars of home building revenue over the next decade.
What’s right?
We were pleased to see Applebaum address the failure of Operation Breakthrough, and the promise of Canada’s Rapid Housing Initiative. He correctly noted that the volatility of the housing market will always threaten overly-rigid manufacturing production types. Government stimulus of off-site businesses can fast-track change by lowering prices for better quality housing while shielding the young industry from sharp downturns.
What’s a miss?
The article focused on the housing crisis (demand-side) and the pressures on manufacturers (supply-side) without addressing the 100-year old go-to-market problem modular has faced in the US. The issue is that the way of doing business has to change along with the way we produce housing. For example, the trades – builders, plumbers, electricians – profit greatly through traditional on-site construction practices. Modular production can offer a new way of doing business that can empower them to increase profit with less grind.
Skye Morse, a Vermont-based multifamily housing developer addresses the need for a new approach to building that creates more “velocity” in his projects.
“We need to conceptualize, design, fund, and build more quickly. Three years of development followed by 18 months of construction is simply too long.”
Like most developers, Morse’s projects must be reviewed, bid, and administered by these builders, whose primary skill set is in the trades – not project administration. Additionally, Jacob Smith, an early investor in LOGIC echoes the need for a building revolution:
“We can’t continue to build the way we have for the last 100 years and expect different results. LOGIC’s combination of approaches promises to be different. Their modular, off-site manufactured solutions can help make comfortable and eco-friendly housing available to millions of people around the world, and thousands closer to home…”
Smith goes on to highlight a key shift in what modular has been missing for decades, “…[LOGIC’s] software-oriented delivery system promises to enable lots of builders to realize more homes, with less toil…” Thankfully, LOGIC is developing 21st-Century software to provide an organized, predictable, controllable, data-rich installer network. These professionals know the job to be done, they know the product, and they know how to deliver what will work for customers.
Modular has always been the answer. LOGIC makes it the solution. Join us as a customer, investor, or collaborator to revolutionize home building.
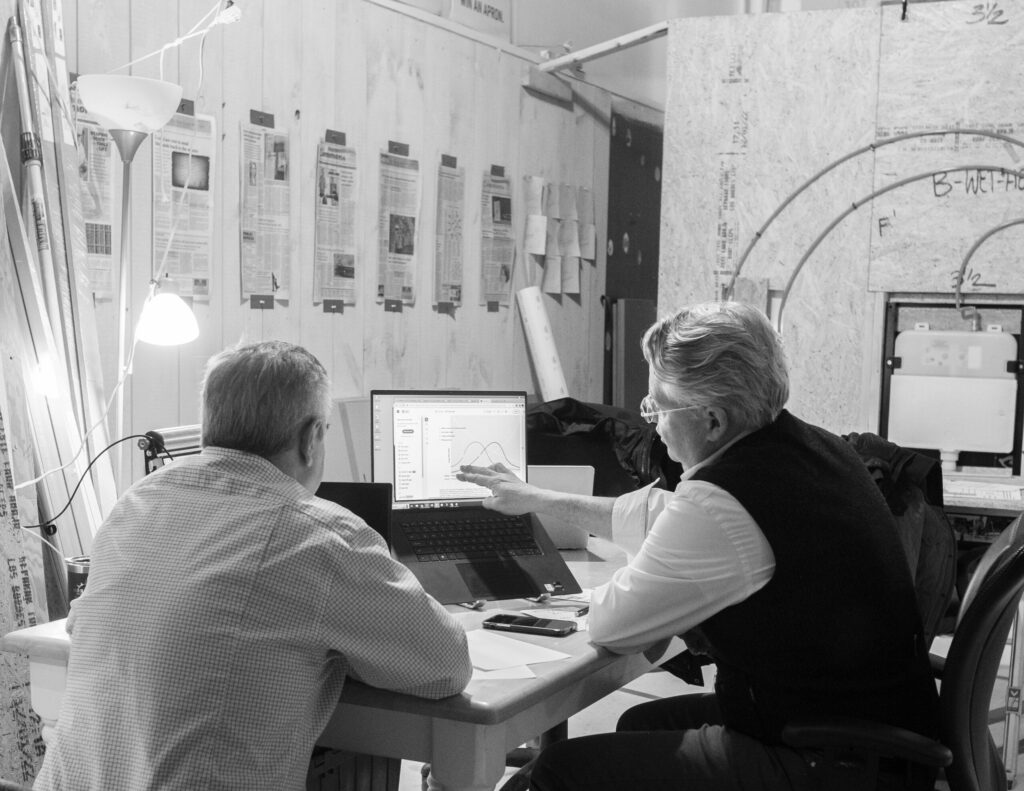
Jason Van Nest is the Founder and CEO of LOGIC Building Systems, and a professor of Architecture at the New York Institute of Technology.